Gifts of Rock: AI has been taught to separate rich and poor ores

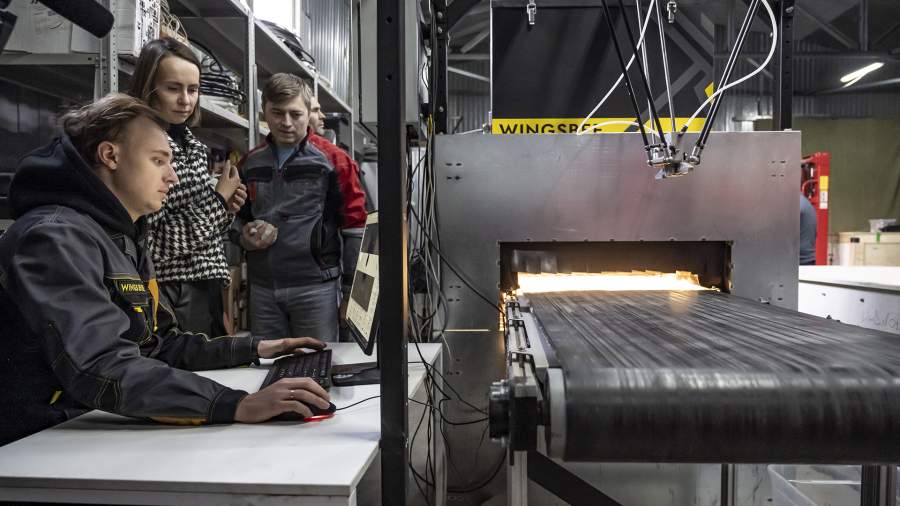
Russia has developed a sample installation that recognizes useful minerals in ore using X-rays and artificial intelligence. The equipment analyzes the rock based on data on the internal structure of the samples. According to the developers, the accuracy of the analysis exceeds 98%, and productivity is up to several tens of tons per hour, depending on the specifics of production. The plant will enrich a wide range of ore raw materials, including precious and rare earth metals.
How ore is enriched using AI
Engineers from the Ural State Mining University (UGGU) have developed the country's first plant for the enrichment of minerals using X-rays and artificial intelligence. The machine belongs to the XRT separator class. This equipment is designed to separate valuable minerals from "waste rock" based on the difference in the transmission properties of X-rays.
As the experts explained, the principle of operation of the separator is similar to the process of fluorography of living organisms. The device X-rays the pieces of rock that move along the conveyor, and determines from the image whether they contain valuable components. The analysis is performed using AI algorithms.
— Each mineral has its own unique X-ray "signature". It depends on the density of the rock and its chemical composition. In our case, machine vision decides where to sort the material — to concentrates or tailings (waste rock) — with an accuracy of more than 98%," Igor Vlasov, one of the developers and a senior researcher at the UGSU Research Laboratory Center, told Izvestia.
He noted that XRT separation is used all over the world, but so far domestic enterprises have used foreign equipment. At the same time, in the development of UGSU, unlike its analogues, the neural network simultaneously studies the "pattern" of the rock and measures the depth of radiation absorption. Thus, the decision is made not only by analyzing the shades of black and white on X-rays, as in most similar devices, but also based on the internal geometry of the sample.
What is the difference between the industrial installation option
According to the specialist, at the moment, the developed laboratory complex includes a conveyor belt about a meter wide, and the rock is sorted by a robotic arm. She needs time to capture and transfer samples to the appropriate containers. Therefore, the equipment has low productivity.
In the industrial version, the separation of the rock will be carried out by a pneumatic system. It consists of a multitude of small nozzles in which compressed air is concentrated. The valves will be opened using artificial intelligence. At the right moment, the mechanisms will begin to "shoot" the empty rock aside. The width of the conveyor belt will be about 5 m. The estimated productivity of such an installation is up to several tens of tons of rock per hour.
— The technological efficiency of the XRT method has been proven, in particular, for ore raw materials of non—ferrous, ferrous, noble, rare earth and precious metals. The results of our research also showed that the proposed complex can separate a wide range of ores. Currently, the development is at the stage of digital learning, for which a large database is being created, in which various types of minerals are classified," Igor Vlasov said.
He explained that in the future, the neural network will sort samples according to the specified criteria that take into account the conditions of specific industries. It is assumed that for this purpose, developers will work closely with specialists of enterprises at the stage of further training of the program.
— Artificial intelligence offers a variety of possibilities. It can also be used to optimize production processes by tracking, for example, the movement of various objects. Neural networks can also predict equipment failures, monitor product quality, and monitor compliance with safety standards," Anna Pyataeva, head of the Artificial Intelligence Center at Siberian Federal University, told Izvestia.
According to her, delegating these functions to artificial intelligence enables enterprises to save on performing routine operations.
In turn, Alexey Korovin, senior researcher at the New Materials Design group at the AIRI Institute, noted that the prospects for implementing AI algorithms can cover most parts of production chains. Including in the field of mining, these tools are used in geological exploration, mining automation, and ore processing. At the same time, an equally important aspect is the use of artificial intelligence algorithms to develop new processes and materials that are obtained from both minerals themselves and related products.
— The very concept of artificial intelligence is widely interpreted, — said the director of the engineering company, which serves mining enterprises, Dmitry Podkamenny. — At the same time, it should be borne in mind that these algorithms are inherently stochastic, that is, based on a random sample of data.
Therefore, when implementing such tools, the probability of errors should be taken into account, therefore, responsibility for possible consequences should be distributed in advance and mechanisms for compensating for "mistakes" of artificial intelligence should be created, the expert concluded.
Переведено сервисом «Яндекс Переводчик»