With the precision of a robot: how Russian enterprises are heading for automation

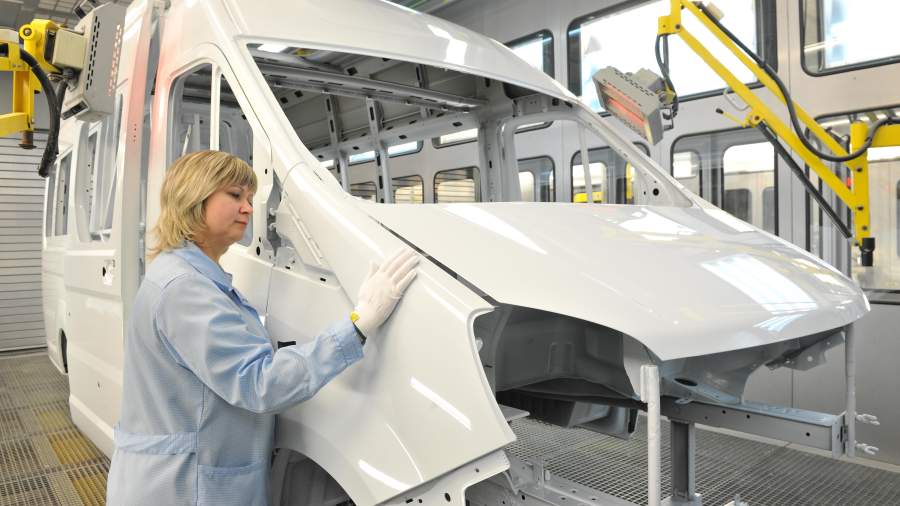
Russia today has an ambitious goal — to enter the top 25 countries in terms of robotics density by 2030. To do this, enterprises need to install more than 100,000 robots in addition to the existing 13,000. The main risk for businesses is that all the work can come down to chasing numbers. To prevent this from happening, you need to be clearly aware of what automation is for. The main goal is, of course, to increase labor productivity and efficiency. But, as the experience of leaders shows, changes can be more extensive and affect not only operational performance, but also the quality of the final product and processes. About what steps domestic enterprises are taking to increase automation and what successes have already been achieved — in the material of Izvestia.
Ambitious plans
The task of making Russia one of the leading countries in terms of industrial robotization is outlined in President Vladimir Putin's decree on national development goals dated June 7, 2024. The implementation of this task assumes that for every 10,000 workers in Russia there will be 100 robots. In general, domestic enterprises will have to introduce more than 100 thousand robots into their processes — now, according to estimates by the Institute for Statistical Research and Economics of Knowledge (IIEZ) in 2023, there are only 12.8 thousand of them.
The federal project "Development of industrial robotics and production Automation", which has become part of the new national project "Means of Production and Automation", overseen by the Ministry of Industry and Trade, is aimed at solving a large-scale task. In these documents, the bar is even higher: by 2030, the country should have 145 robots for every 10,000 workers.
Today, industrial regions are expected to lead in the number of robots: St. Petersburg, Samara, Moscow, Kaluga and Nizhny Novgorod regions, Tatarstan. As IIEZ analysts point out, despite the differences in the structure of the use of robots, in all these regions of the Russian Federation there are automotive sites producing cars, trucks, and buses.
Indeed, the automotive industry is considered one of the most highly automated industries in the country: in the face of fierce competition with foreign suppliers, the introduction of the most up-to-date world-class technical solutions began here earlier than in other sectors. For example, the automobile plant in Nizhny Novgorod currently employs 583 industrial robots, which in relation to the number of employees is 290 robots per 10,000 people. This is comparable to the indicators of the whole region: for example, in the entire Sverdlovsk region, according to IIEZ calculations, 505 industrial robots are used.
The goal determines the means
In today's shortage of personnel, automation is necessary to remove some of the tasks from a person and thus increase labor productivity and efficiency. Robots, of course, contribute to all this in some areas, but, as the experience of leaders shows, with more ambitious goal setting and system implementation, the results will be more impressive.
Ten years ago, Gorky Automobile Plant began automating its processes, and at the same time, the company was actively building its own production system and adopting the best international practices in quality management. The changes did not begin with the updating of hardware — first of all, they changed the nature of production and the thinking of employees. The essence of the new approach, which was formulated by industrialist Oleg Deripaska, was the thesis "The salary is paid by the buyer," which is still at the forefront here.
"The primary thing was to change the business philosophy itself, and robots, modern machines and measuring instruments became just a tool on the way to a new goal — to make a car that employees themselves could be proud of," Andrey Sofonov, director of the Nizhny Novgorod Automobile Plant, told Izvestia.
Production with a scientific approach
Oleg Deripaska, a graduate of the Moscow State University Faculty of Physics, laid down the key principles of academic science as the basis for all changes in production.
— The scientific approach is the most attractive thing for me in this management system. Because, like any science, it can be hard-worked to comprehend, develop, replicate, and subordinate the work of each link in our production to its logic. Like any scientific method, it can be creatively developed and improved," the industrialist said.
This was also the case with automation: all technical innovations were introduced consistently and gradually, focusing on the main goal — improving the quality of the final product and processes. The first robots in the production of the legendary "Gazelles" and "Sables" appeared on the welding lines of bodies and cabins. Today, 85% of operations in these areas are performed automatically.
— The intelligent control system fully controls the process. The manipulator robots move the parts to the welding robots quickly and precisely in a specific order. The system automatically detects the modification of the vehicle. This allows you to weld different body modifications in one flow," explains Andrey Matyasov, head of the welding production at the automobile plant.
The reliability of welded joints is checked in the destructive testing laboratory. There, experts evaluate not only the length of the seam and the distance between the welded points, but also the so-called core diameter, which characterizes the strength of the joint. This is followed by painting, or rather, a whole range of work from surface preparation and priming to applying paint and varnish coating.
— Our paint complex is one of the most modern in the country. Its software allows you to monitor more than 200 parameters online - the operation of equipment, including unique robots, the physical and chemical properties of materials, the microclimate in the workshop, painting time, and so on," says Dmitry Veremeev, manager of the paint production.
The new equipment in the paint complex helped the automobile plant to overcome the main stereotype about "Gazelles", which remained from the Soviet past. Rust is no longer a concern for owners of modern Nizhny Novgorod trucks: galvanized steel and new technologies of cataphoretic priming have increased the guarantee for the absence of end-to-end corrosion to 12 years.
Apart from the unmanned platforms for delivering components running in various directions on the assembly line (although they already cover 41 routes and transport 554 types of parts), there are no robotic manipulators as such, but modern technical solutions help ensure the quality of the final product.
— Control points are built into the assembly process — this is the so-called built-in quality. The supervisors check the compliance of all works with the design documentation on them. For example, before boarding the cab, all connections are monitored, access to which will be difficult later," says Igor Krasnov, truck production manager.
Ready-made cars are already being tested "on the move", on a special track: they check the car's handling and stability on eight sections, including the "Belgian pavement", "cobblestone", "wave", sudden acceleration and braking on a flat road section, then the electrical systems are checked. But that's not all — then the machines are sent for a consumer-facing audit (CSA).
— CSA auditors are trained to behave exactly how clients behave. They check the joints of the panels, the quality of the paintwork, and look under the hood. If the auditor "won't buy" a freshly assembled car because of the assembly comments, then the real customer won't buy it either," emphasizes Igor Krasnov.
Quality as a process
A special approach to quality and the same "consumer's view" is important not only in production — it permeates all stages of the car factory, from design to interaction with dealers. Engineers develop new products using the Quality Gate system (PPDS), based on market requirements, and control the ratio of quality and cost at each design stage. The procurement system is also organized in such a way that the car factory buys not just a specific part from suppliers, but evaluates the production process. This ensures the quality of each batch.
A newly created intelligent complaints management system (RMS) helps to quickly solve emerging problems, which brings production, sales system, after-sales service and suppliers into a single IT network.
— Warranty repair certificates are issued in the IT platform, and it is also possible to automate the creation and timely submission of claims to suppliers of components, and generate online reports. All claims work with suppliers is currently conducted only through this system, which makes it possible to increase the speed of problem solving and ultimately contributes to customer satisfaction," explains Nadezhda Gvozdkova, Chief Specialist of the company's Quality Directorate.
From the point of view of applying modern digital solutions, the Nizhny Novgorod Automobile Plant case is an example of an integrated approach. For example, in 2023, with the support of the Russian Information Technology Development Fund, the automobile plant began implementing a digital project for integrated product lifecycle and production process management. Today, 190 pieces of equipment have already been connected to the unified digital system at the plant.
— The digital dispatcher records the condition of the machines in real time, monitors all telemetry parameters — voltage, power, temperature, vibrations and notifies the operator of the need to make adjustments. This helped to increase the efficiency of using the technology park by 15%," says Elena Smirnova, director of the Center for IT Solutions for Business at the automobile plant.
At the same time, the company is working on the creation of a PLM platform (Product Lifecycle Management), which reduces the development time of new car models and allows collecting generalized information about the operation of each model in the market in order to make improvements to the model range based on it.
Federal level assessment
The results of this work can be assessed on a case-by-case basis, but there is also one effect common to all employees of the automobile plant: despite the massive expansion of the Chinese automotive industry, the company consistently holds over 50% of the Russian LCV market.
It is also important that the path that the automobile plant has taken in working on itself and its products is highly appreciated not only by the market. By the end of 2024, the company became the winner of the quality award of the Government of the Russian Federation. As part of the competition, Roskachestvo experts conduct a comprehensive assessment of enterprises' performance based on various criteria: leadership, strategy, personnel, partnership, products, services, and key results. In fact, this is a comprehensive assessment of the business management model, and Nizhny Novgorod Automobile Plant received the highest score. Robots serve people here, not the other way around— that's probably the secret.
Переведено сервисом «Яндекс Переводчик»