С точностью робота: как российские предприятия держат курс на автоматизацию

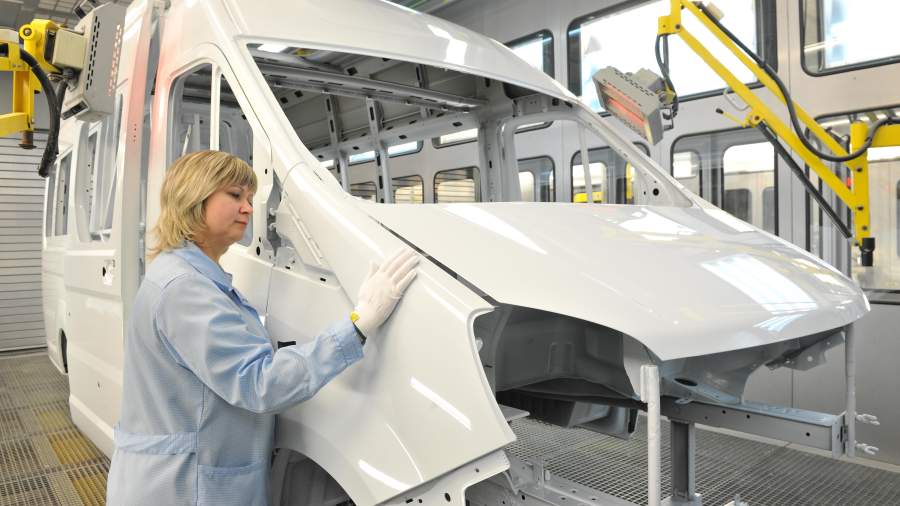
Перед Россией сегодня стоит амбициозная цель — к 2030 году войти в топ-25 стран по плотности роботизации. Для этого на предприятиях необходимо установить более 100 тыс. роботов в дополнение к уже существующим 13 тыс. Главный риск для предприятий заключается в том, что вся работа может свестись к погоне за цифрами. Чтобы этого не произошло, нужно четко осознавать, ради чего затевать автоматизацию. Основная цель — это, безусловно, повышение производительности труда и эффективности. Но, как показывает опыт лидеров, изменения могут быть масштабнее и влиять не только на операционные показатели, но и на качество конечного продукта и процессов. О том, какие шаги отечественные предприятия предпринимают по повышению автоматизации и каких успехов уже удалось добиться — в материале «Известий».
Амбициозные планы
Задача вывести Россию в число ведущих государств по показателю роботизации промышленности обозначена в указе президента Владимира Путина о национальных целях развития от 7 июня 2024 года. Реализация этой задачи предполагает, что на каждые 10 тыс. работников в России будет приходиться 100 роботов. В целом отечественным предприятиям предстоит внедрить в свои процессы более 100 тыс. роботов — сейчас их, по подсчетам Института статистических исследований и экономики знаний (ИСИЭЗ) за 2023 год, лишь 12,8 тыс.
На решение масштабной задачи нацелен федеральный проект «Развитие промышленной робототехники и автоматизации производства», ставший частью нового нацпроекта «Средства производства и автоматизации», который курирует Минпромторг. В этих документах планка еще выше: к 2030 году в стране должно быть 145 роботов на каждые 10 тыс. работников.
Сегодня по количеству роботов ожидаемо лидируют промышленные регионы: Санкт-Петербург, Самарская, Московская, Калужская и Нижегородская области, Татарстан. Как указывают аналитики ИСИЭЗ, несмотря на различия в структуре применения роботов, во всех этих субъектах РФ есть автомобилестроительные площадки, выпускающие легковые и грузовые автомобили, а также автобусы.
Автопром, действительно, считается одной из самых высоко автоматизированных отраслей в стране: в условиях жесткой конкуренции с зарубежными поставщиками здесь раньше, чем в других секторах, началось внедрение самых актуальных технических решений мирового уровня. Например, на автозаводе в Нижнем Новгороде сегодня задействовано 583 промышленных робота, что в соотношении к численности работников составляет 290 роботов на 10 тыс. человек. Это сопоставимо с показателями целого региона: так, во всей Свердловской области, согласно подсчетам ИСИЭЗ, применяют 505 промышленных робота.
Цель определяет средства
В сегодняшних условиях дефицита кадров автоматизация необходима, чтобы снять часть задач с человека и таким образом повысить производительность труда и эффективность. На отдельных участках всему этому роботы, конечно, способствуют, но, как показывает опыт лидеров, при более масштабном целеполагании и системном внедрении и результаты будут более впечатляющими.
Десять лет назад Горьковский автозавод начал автоматизировать свои процессы, и параллельно с этим на предприятии активно строили собственную производственную систему и перенимали лучшие мировые практики в управлении качеством. Перемены начались не с обновления «железа» — прежде всего меняли характер производства и мышление сотрудников. Суть нового подхода, которую сформулировал промышленник Олег Дерипаска, заключалась в тезисе «Зарплату платит покупатель», который и сейчас здесь во главе угла.
— Первичным было изменение самой философии бизнеса, а роботы, современные станки и измерительные приборы стали просто инструментом на пути к новой цели — делать такой автомобиль, которым могли бы гордиться сами сотрудники, — рассказал «Известиям» директор Нижегородского автозавода Андрей Софонов.
Производство с научным подходом
В основу всех изменений на производстве Олег Дерипаска, выпускник физфака МГУ, заложил ключевые принципы академической науки.
— Научность подхода — самое привлекательное для меня в этой системе менеджмента. Потому что, как и любую науку, ее можно упорным трудом постичь, развить, тиражировать, ее логике подчинять работу каждого звена нашего производства. Как и любой научный метод, его можно творчески развивать и совершенствовать, — говорил промышленник.
Так было и с автоматизацией: все технические новинки внедряли последовательно и постепенно, ориентируясь на главную цель — повышение качества конечного продукта и процессов. Первые роботы на производстве легендарных «Газелей» и «Соболей» появились на линиях сварки кузовов и кабин. Сегодня уже 85% операций на этих участках выполняется в автоматическом режиме.
— Интеллектуальная управляющая система полностью контролирует процесс. Роботы-манипуляторы быстро и точно в определенно заданном порядке перемещают детали к сварочным роботам. Система автоматически определяет модификацию автомобиля. Это позволяет в одном потоке сваривать разные модификации кузовов, — объясняет управляющий сварочным производством автозавода Андрей Матясов.
Надежность сварных соединений проверяют в лаборатории разрушающего контроля. Там специалисты оценивают не только длину шва и расстояние между сварными точками, но и так называемый диаметр ядра, который характеризует прочность соединения. Дальше следует окраска, а точнее — целый комплекс работ от подготовки поверхности и грунтования до нанесения лакокрасочного покрытия.
— Наш окрасочный комплекс — один из самых современных в стране. Его программное обеспечение позволяет в онлайн-режиме отслеживать более 200 параметров — работу оборудования, в том числе уникальных роботов, физические и химические свойства материалов, микроклимат в цеху, время окраски и так далее, — комментирует управляющий окрасочным производством Дмитрий Веремеев.
Новое оборудование в окрасочном комплексе помогло автозаводу побороть главный стереотип о «Газелях», оставшийся с советского прошлого. Владельцев современных нижегородских грузовиков ржавчина больше не беспокоит: оцинкованная сталь и новые технологии катафорезного грунтования позволили увеличить гарантию на отсутствие сквозной коррозии до 12 лет.
На сборочном конвейере, если не считать курсирующие в различных направлениях беспилотные платформы для доставки компонентов (хотя они охватывают уже 41 маршрут и перевозят 554 вида деталей), роботов-манипуляторов как таковых нет, но современные технические решения помогают обеспечивать качество конечного продукта.
— В сборочный процесс встроены контрольные точки — это так называемое встроенное качество. На них контролеры проверяют соответствие всех работ конструкторской документации. Например, перед посадкой кабины контролируются все соединения, доступ к которым будет впоследствии затруднен», — рассказывает управляющий производством грузовых автомобилей Игорь Краснов.
Готовые машины испытывают уже «на ходу», на специальном треке: проверяют управление автомобилем и его устойчивость на восьми участках, включая «бельгийскую мостовую», «булыжник», «волну», резкий разгон и торможение на участке ровной дороги, затем идет проверка работоспособности электрических систем. Но и это еще не всё — затем машины отправляются на аудит глазами потребителя (CSA).
— Аудиторы CSA обучены вести себя именно так, как ведут себя клиенты. Они проверяют стыки панелей, качество лакокрасочного покрытия, заглядывают под капот. Если аудитор «не купит» свежесобранную машину из-за замечаний к сборке, то ее не купит и реальный клиент, — подчеркивает Игорь Краснов.
Качество как процесс
Особый подход к качеству и тот самый «взгляд потребителя» важен не только при производстве — он пронизывает на автозаводе все этапы, от проектирования до взаимодействия с дилерами. Инженеры разрабатывают новые продукты по системе «Ворота качества» (PPDS), отталкиваясь от требований рынка, и на каждом этапе проектирования контролируют соотношение качества и стоимости. Система закупок тоже организована так, что автозавод покупает у поставщиков не просто конкретную деталь, а оценивает процесс ее производства — это позволяет гарантировать качество каждой партии.
Быстро решать возникающие проблемы помогает созданная недавно интеллектуальная система управления рекламациями (СУР), которая заводит в единую ИТ-сеть производство, систему продаж, послепродажное обслуживание и поставщиков.
— В ИТ-платформе оформляются акты гарантийных ремонтов, также там можно автоматизировать создание и своевременное выставление претензий поставщикам комплектующих, формировать онлайн-отчеты. Вся претензионная работа с поставщиками сейчас ведется только через эту систему, что дает возможность повышать скорость решения проблем и в конечном итоге способствует удовлетворенности клиентов, — поясняет главный специалист дирекции по качеству предприятия Надежда Гвоздкова.
С точки зрения применения современных цифровых решений кейс Нижегородского автозавода — пример комплексного подхода. Например, при поддержке Российского фонда развития информтехнологий в 2023 году автозавод начал внедрять цифровой проект комплексного управления жизненным циклом продукта и производственными процессами. Сегодня к единой цифровой системе на заводе уже подключено 190 единиц оборудования.
— Цифровой диспетчер фиксирует состояние станков в режиме реального времени, контролирует все параметры телеметрии — напряжение, мощность, температуру, вибрации и оповещает оператора о необходимости внесения корректировок. Это помогло повысить эффективность использования технологического парка на 15%, — рассказывает директор Центра ИТ-решений для бизнеса автозавода Елена Смирнова.
Параллельно предприятие работает над созданием PLM-платформы (Product Lifecycle Management — управление жизненным циклом продукта), сокращающей сроки разработки новых моделей автомобилей и позволяющей собирать обобщенную информацию об эксплуатации каждой модели в рынке, чтобы на ее основе вносить улучшения в модельный ряд.
Оценка федерального уровня
Результаты этой работы можно оценить на каждом конкретном участке, но есть и один общий для всех сотрудников автозавода эффект: несмотря на массированную экспансию китайского автопрома, предприятие стабильно держит свыше 50% российского рынка LCV.
Важно и то, что путь, который прошел автозавод в работе над собой и своими продуктами, высоко оценивает не только рынок. По итогам 2024 года предприятие стало лауреатом премии качества правительства РФ. В рамках конкурса эксперты Роскачества проводят всестороннюю оценку деятельности предприятий по различным критериям: лидерство, стратегия, персонал, партнерство, продукция, услуги, ключевые результаты. По сути, это всеобъемлющая оценка модели управления бизнесом — и нижегородский автозавод получил высший балл. Здесь роботы служат людям, а не наоборот — наверное, в этом секрет.